How to Set a Torque Wrench Properly
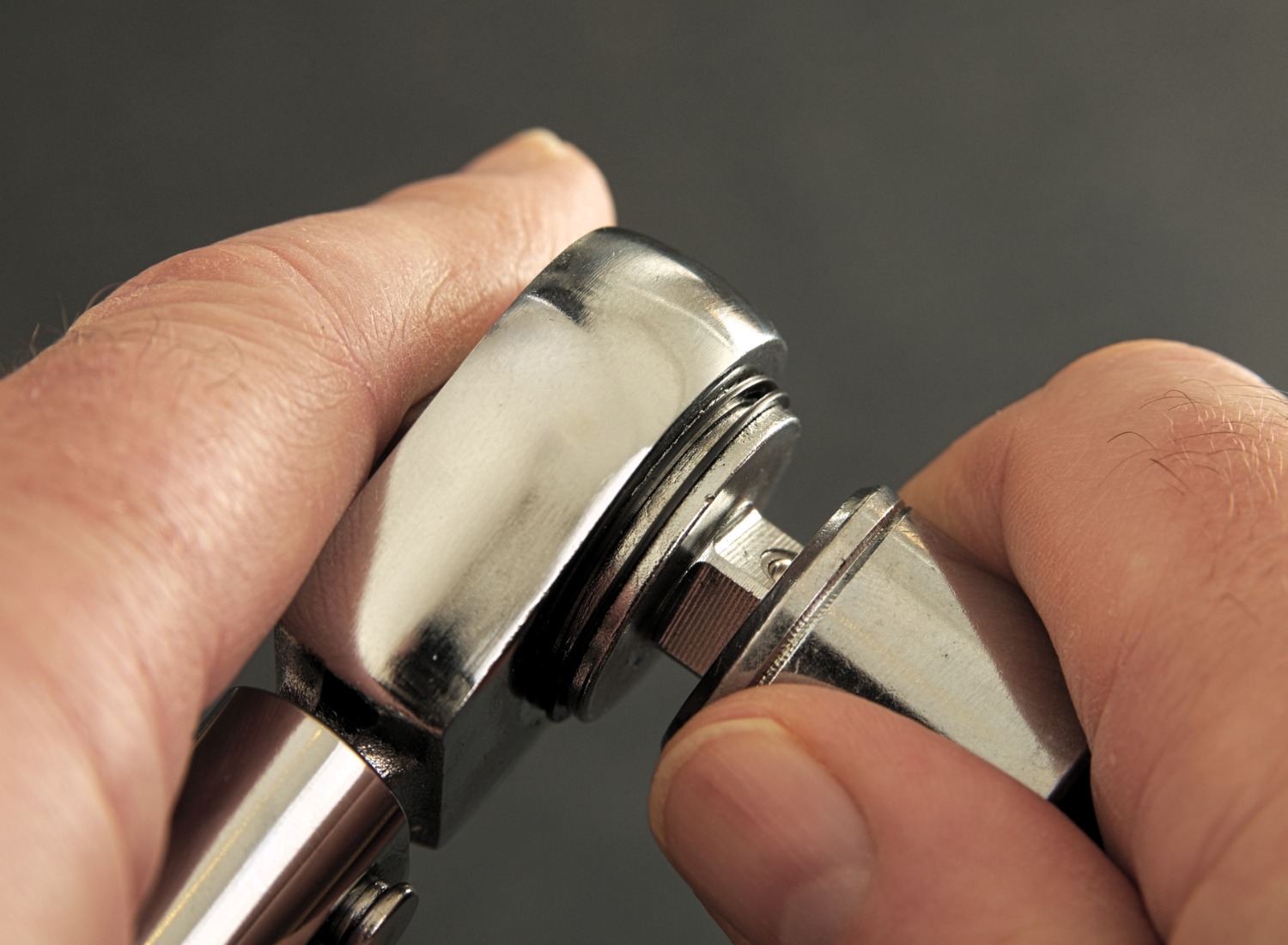
In the world of mechanics and do-it-yourself enthusiasts, precision is paramount. The art of tightening bolts and nuts to just the right degree can mean the difference between a successful repair and a catastrophic failure. Enter the trusty torque wrench, a tool designed to provide exacting control over torque application. Whether you’re working on a car engine, assembling furniture, or tackling any project involving fasteners, knowing how to set a torque wrench correctly is essential.
This blog will be your comprehensive guide to mastering this crucial skill. We’ll delve into the fundamentals of torque, explore the types of torque wrenches available, and walk you through the critical steps of calibration and proper torque setting. By the time you finish reading, you’ll know to ensure accurate and consistent fastener tightening every time you pick up your torque wrench.
Understanding Torque
Before setting a torque wrench, it’s crucial to grasp the concept of torque. Torque measures rotational force typically expressed in units like pound-feet (lb-ft) or Newton meters (Nm). When you tighten a bolt or nut, you’re applying torque to it. Too much torque can damage the fastener or the material securing, while too little torque may result in a loose connection.
Selecting the Right Torque Wrench
The first step in setting a torque wrench properly is choosing the right tool for the job. Torque wrenches come in various types, including beam-type, click-type, and digital torque wrenches. Each type has its own advantages and limitations. Still, a click-type torque wrench is a popular choice for most automotive and general mechanical applications due to its reliability and ease of use.
Ensure that the torque wrench you select has a suitable torque range for the task at hand. Using a torque wrench at the extremes of its range can reduce accuracy. For instance, if you need to tighten a bolt to 50 lb-ft, it’s best to use a torque wrench with a range of 20-100 lb-ft rather than one with a range of 10-50 lb-ft.
Calibrating Your Torque Wrench
Calibration is crucial to ensure the accuracy of your torque wrench. Over time, torque wrenches can become inaccurate due to wear and tear, mishandling, or exposure to extreme conditions. To calibrate your torque wrench, follow these steps:
- Consult the manufacturer’s instructions: Refer to the manufacturer’s instructions for your specific torque wrench model. These instructions will guide calibration procedures and recommended intervals.
- Use a torque calibration device: You’ll need a torque calibration device designed to apply a known and precise amount of torque. This device is essential for verifying the accuracy of your torque wrench.
- Adjust the wrench: Most torque wrenches have an adjustment knob or screw that allows you to fine-tune the torque setting. Set the torque wrench to the lowest end of its range to ensure accuracy during calibration.
- Apply force: Attach the torque calibration device to your torque wrench and apply the specified torque, following the manufacturer’s instructions. The torque wrench should click or signal when it reaches the set torque. If it doesn’t, use the adjustment knob or screw to make the necessary corrections until it does.
- Repeat if necessary: For added assurance, repeat the calibration process a few times to ensure consistency. It may be time to replace or service your torque wrench if you find significant discrepancies.
Setting the Desired Torque
Once you calibrate your torque wrench, you can set the desired torque for your fastening task. Follow these steps:
- Know your torque specification: Consult the manufacturer’s specifications or guidelines for the fastener you’re working with to determine the recommended torque. This information is crucial for preventing over-tightening or under-tightening.
- Set the wrench: Adjust your torque wrench to the desired torque setting. Most click-type torque wrenches have a scale or dial that allows you to select the desired torque level. Ensure that the scale lines up with the correct value.
- Test the wrench: Before using the torque wrench on your workpiece, test a scrap piece of material or in a controlled environment to ensure the wrench clicks or signals accurately at the set torque.
- Apply torque gradually: When using the torque wrench, apply torque gradually and steadily. Avoid sudden jerks or quick movements, as this can affect the accuracy of the reading.
- Listen for the click: As you apply torque, listen for the audible click or feel for the tactile signal from the torque wrench. This indicates that you’ve reached the set torque and should stop tightening immediately.
Maintenance and Storage
Proper maintenance and storage are essential to keep your torque wrench in good working condition. After use, always set the torque wrench back to its lowest setting to release tension on the internal components. Store it in a protective case or pouch to prevent damage.
Final Thoughts
Setting a torque wrench properly is a fundamental skill for anyone working with fasteners. It ensures that you achieve the desired level of tightness while preventing potential damage or safety risks. Remember to select the right torque wrench, calibrate it regularly, and follow the manufacturer’s instructions and torque specifications for your specific tasks. By doing so, you’ll maintain the accuracy and reliability of your torque wrench for years to come, making it a valuable asset in your toolbox.