How to Choose the Right Solder for Your Electronics Projects
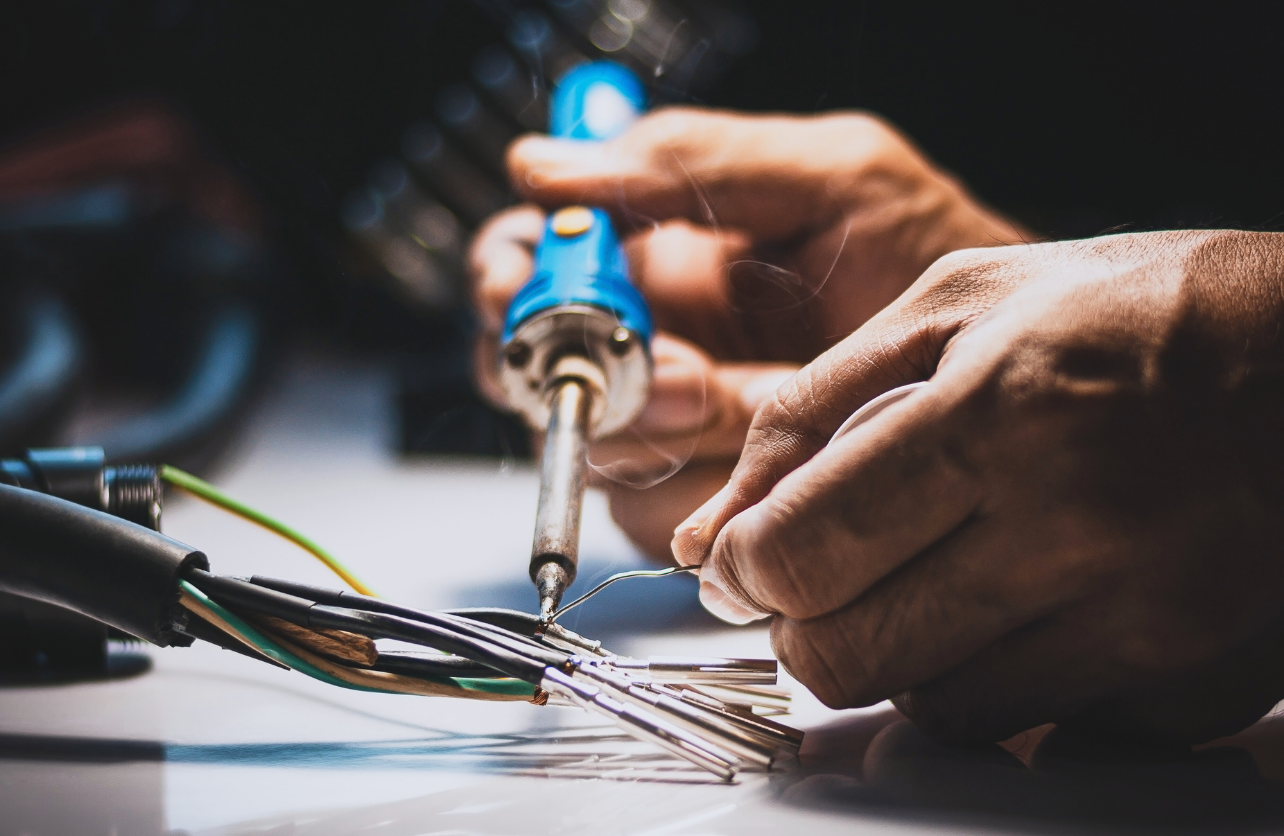
Soldering is a fundamental skill for working with electronics and choosing the right solder is key to creating strong, reliable connections. With a variety of solder types available, it’s essential to understand their differences and when to use each one. This guide will walk you through the most common solder types, their compositions, and their ideal use cases to help you make the best choice for your next project.
Why Choosing the Right Solder Matters
The solder you use directly affects the quality of your connections. A strong joint ensures that your components work correctly and that the circuit remains reliable over time. Using the wrong solder can lead to weak joints, corrosion, or even damage to your components.
Types of Solder for Electronics
Leaded Solder
Composition: A mix of tin (60%) and lead (40%).
Leaded solder has been a long-time favorite among electronics enthusiasts due to its ease of use and reliability. It has a lower melting point than lead-free solder, making it easier to work with, especially for beginners.
Best Use Cases:
- Prototyping and hobby projects.
- Repairs and rework on older electronics.
Pros:
- Easier to melt and flow.
- Produces smooth, reliable joints.
- More forgiving for beginners.
Cons:
- Contains lead, which is toxic. Requires proper ventilation and safety precautions.
- Prohibited in many industries due to environmental and health regulations.
Lead-Free Solder
Composition: Typically tin combined with other metals like silver or copper.
Lead-free solder is now the industry standard, especially in commercial electronics, due to environmental regulations like RoHS (Restriction of Hazardous Substances). While it’s more eco-friendly, lead-free solder requires higher temperatures and can be slightly harder to work with.
Best Use Cases:
- Commercial and industrial electronics.
- Projects where environmental compliance is necessary.
Pros:
- Safer for the environment and health.
- Required for projects intended for sale in regulated markets.
Cons:
- Higher melting point makes it more challenging for beginners.
- Joints may appear duller compared to leaded solder.
Rosin-Core Solder
Composition: Can be leaded or lead-free, with a core containing rosin flux.
Rosin-core solder is designed for electronics, as the flux inside the solder wire helps clean the joint during soldering, improving adhesion and conductivity. It eliminates the need to apply flux separately, simplifying the process.
Best Use Cases:
- Circuit boards and delicate electronic components.
- Projects requiring clean and efficient soldering.
Pros:
- Built-in flux makes soldering more efficient.
- Reduces oxidation during soldering.
Cons:
- Can leave behind residue that may need cleaning.
Silver-Bearing Solder
Composition: Tin with a small percentage of silver (typically 2-4%).
Silver-bearing solder is prized for its strength and conductivity. It’s often used in high-performance electronics or where durability is critical.
Best Use Cases:
- High-end audio equipment.
- Applications requiring robust, long-lasting joints.
Pros:
- Stronger joints than standard tin-lead solder.
- Excellent electrical conductivity.
Cons:
- More expensive than other types of solder.
- Higher melting point.
Factors to Consider When Choosing Solder
- Project Type:
- For hobby projects or repairs, leaded solder is often the easiest to work with.
- For commercial projects, lead-free solder may be required by law.
- Component Sensitivity:
- Use rosin-core solder for delicate components, as it reduces the need for additional flux.
- Environmental Concerns:
- Opt for lead-free solder to minimize environmental impact and comply with regulations.
- Skill Level:
- Beginners may find leaded solder easier to handle due to its lower melting point.
- Tools Available:
- Lead-free and silver-bearing solders require higher temperatures, so ensure your soldering iron can reach the required heat.
Tips for Using Solder Effectively
- Work in a Well-Ventilated Area: Always solder in a space with good ventilation to avoid inhaling fumes.
- Use the Right Temperature: Match your soldering iron’s heat to the solder type. Too little heat can lead to cold joints, while excessive heat can damage components.
- Clean Joints: Always clean surfaces before soldering for better adhesion.
- Practice Makes Perfect: If you’re new to soldering, practice on spare components to get comfortable with the process.
Conclusion
Choosing the right solder for your electronics project is a small decision with a big impact on your results. Whether you go with leaded solder for its ease of use or opt for lead-free solder for compliance, understanding the pros and cons of each type is key to creating strong, reliable connections. By considering your project’s needs and your skill level, you’ll be well on your way to mastering the art of soldering.